Occupational Health & Safety
At ITC, primary importance is placed on the Occupational Health & Safety of its employees (including that of service providers) and all visitors to our establishments. This is ensured through strict observance of Corporate Environment, Health and Safety Guidelines incorporating best international standards and practices. All ITC establishments are audited by corporate resources and expert third party agencies on a periodic basis to verify compliance. These Reports are reviewed at the Board level.
Towards Zero Accident
All our factories, hotels and large offices have established Environment, Health & Safety (EHS) Management systems with designated roles & responsibilities, competent EHS resources and safety infrastructure, which are under constant upgradation to comply with best international standards. In addition, strong employee involvement is encouraged through participation in suggestions schemes, celebration of EHS events, etc.
A continual process of risk assessment has been institutionalised across Businesses wherein risks are systematically identified and mitigation plans implemented. All new projects and major renovation jobs are reviewed and vetted at the design stage by EHS experts and engineering control measures are implemented along with the project. Pre commissioning audits are also conducted to ensure compliance to all EHS requirements before commissioning.
A comprehensive incidents / accidents reporting system has been established in all Units. These incidents/accidents undergo a thorough investigation for identifying root causes and corrective / preventive measures initiated. The findings and recommendations are also discussed in the Safety Committee meetings to ensure complete management and employee buy in.
In order to disseminate the learning from accidents, the serious accident details, along with root cause analysis and proposed corrective measures are communicated throughout the Company. Thereby, Units are equipped to initiate proactive measures to eliminate/ control similar situations.
Lost Time Accidents, Injury Rate and Lost Day Rate
Lost Time Accidents (LTA) |
|
2010-11 |
12 |
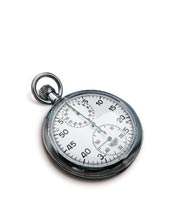 |
2009-10 |
23 |
2008-09 |
15 |
2007-08 |
20 |
2006-07 |
14 |
2005-06 |
16 |
2004-05 |
37 |
2003-04 |
27 |
2002-03 |
35 |
2001-02 |
33 |
LTA - An accident where the
injured does not return to work
in the next scheduled shift |
Lost time Accidents
to ITC employees
brought down to 12 during 2010-11 |
|
All these efforts have yielded excellent results in safety performance during the reporting period. In 2010-11, the number of Lost Time Accidents (LTA) to ITC employees has been brought down to 12, close to half the LTAs in comparison to the previous year, as detailed.
In ITC, Lost Time Accident (LTA) is defined as an accident where the injured is not able to come back to work in the next scheduled shift. This is more stringent than the 'Reportable Accident' as per Factories Act, 1948, which is defined as an accident where injured person is unable to resume duty within 48 hours after the accident.
Injury rate, the frequency of injuries in relation to total time worked has been brought down considerably. The injury rate has been consistently reduced; an improvement of 44% in comparison to 2009-10, despite significant growth in all Businesses.
Lost day rate, defined as number of days lost due to accidents for every 2,00,000 person hours worked, for the year 2010-11 was 2.25 (28.4 in 2009-10).
|